{{flagHref}}
Produits
- Produits
- Catégories
- Blog
- Podcast
- Application
- Document
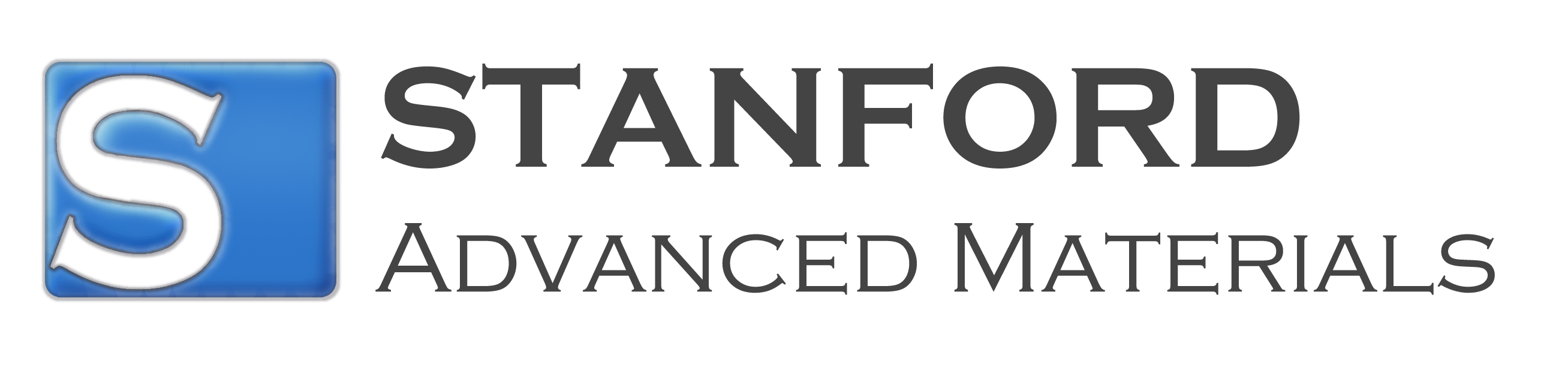
INDUSTRIES
Chimie et pharmacie
Industrie pharmaceutique
Aérospatiale
Agriculture
Automobile
Fabrication de produits chimiques
Dentisterie
Électronique
Stockage d'énergie et batteries
Piles à combustible
Métaux de qualité
Bijoux et mode
Eclairage
Médical
Pétrole et gaz
Optique
Papier et pâte à papier
Produits pharmaceutiques et cosmétiques
Placage
Recherche et laboratoire
Énergie solaire
L'espace
Producteurs d'acier et d'alliages
Équipement sportif
Textiles et tissus
CANDIDATURES
Applications du tungstène
Métallurgie
Semi-conducteurs
Aimants en terres rares
Catalyseur
Poudre d'impression 3D
Poudre d'alliage à haute entropie
Moulage par injection de métal
Fabrication additive
Revêtements par pulvérisation thermique
Pressage isostatique à chaud
Application des terres rares
Catalyseurs environnementaux
Bande de marquage
Matériaux OLED
Fil de thermocouple
Garnitures et internes
Batteries Li-ion et produits chimiques électroniques
Poudres métalliques pour outils diamantés
Poudre magnétique douce
CENTRE DE RECHERCHE
Blogs
Écrire pour nous
Podcast
Certificats d'analyse (COA)
Brochures
Convertisseurs et calculatrices
Recherche de produits
À propos de nous
Services personnalisés
Solutions d'emballage
Essais de matériaux
Promotions actuelles
Profil de l'entreprise
Nouvelles de l'industrie
Expositions
Conditions générales d'utilisation
Politique de confidentialité

-
- Chimie et pharmacie
- Industrie pharmaceutique
- Aérospatiale
- Agriculture
- Automobile
- Fabrication de produits chimiques
- Dentisterie
- Électronique
- Stockage d'énergie et batteries
- Piles à combustible
- Métaux de qualité
- Bijoux et mode
- Eclairage
- Médical
- Pétrole et gaz
- Optique
- Papier et pâte à papier
- Produits pharmaceutiques et cosmétiques
- Placage
- Recherche et laboratoire
- Énergie solaire
- L'espace
- Producteurs d'acier et d'alliages
- Équipement sportif
- Textiles et tissus
-
- Applications du tungstène
- Métallurgie
- Semi-conducteurs
- Aimants en terres rares
- Catalyseur
- Poudre d'impression 3D
- Poudre d'alliage à haute entropie
- Moulage par injection de métal
- Fabrication additive
- Revêtements par pulvérisation thermique
- Pressage isostatique à chaud
- Application des terres rares
- Catalyseurs environnementaux
- Bande de marquage
- Matériaux OLED
- Fil de thermocouple
- Garnitures et internes
- Batteries Li-ion et produits chimiques électroniques
- Poudres métalliques pour outils diamantés
- Poudre magnétique douce
-
- Blogs
-
Écrire pour nous
- Podcast
- Certificats d'analyse (COA)
- Brochures
-
Convertisseurs et calculatrices
- Recherche de produits
- À propos de nous
- Services personnalisés
- Solutions d'emballage
- Essais de matériaux
- Promotions actuelles
- Profil de l'entreprise
- Nouvelles de l'industrie
- Expositions
- Conditions générales d'utilisation
- Politique de confidentialité